The annual cold flow conundrum
Well it’s that time of the year again, the overcoats are being thrown on in the Northern Hemisphere and the clocks have changed and in the world of Bunkering this means only one thing, it’s time to consider Cold Flow properties again.
Why is this so concerning? Winter comes once a year and Cold Flow is nothing new, but the idiosyncrasies of the Bunker Industry allow fuel blenders to thrive within the ‘grey areas’ with regard quality.
Which other industry allows fuels to be sold on multiple and sometimes obsolete International standards or even local specifications?. Indeed 16 years since the 2005 specification was released we still see this being sold, despite 2010, 2012 and the latest 2017 versions being published.
Worryingly, even the latest 2017 specification does not provide adequate protection for cold flow properties with only the winter specification requiring the seller to report Cloud and Cold Filter Plugging Point rather than specifying a hard limit.
Furthermore it is quite remarkable that even Charter Parties have not been adjusted to the latest specifications and that they don’t mandate the use of winter grade fuels only specifying fit for purpose, a statement no supplier will ever warrant.
So what are the grey areas and how can we prevent these issues impacting the end user?
Issues
In short, not only are things not what they seem, they are not even what they are called!
This statement certainly applies for DMA distillates across a large swathe of North West Europe and the epicenter of ARA ports where blenders have for some years now pushed the envelope using additives to masquerade a summer grade fuel as a winter specification. Indeed whilst there generally are warning signs that we can use to detect such fuels there are exceptions and therefore you cannot assume simply on a pour point result that a fuel is a winter grade which will give you adequate protection.
In understanding the effect of the additives we need first to understand the effects of cooling on a distillate fuel such as DMA.
The Cooling Process
As a distillate cools down the first point of note is what is known as the Cloud Point, this is the temperature under laboratory conditions at which wax crystals in the fuel become visible by way of the first wisps of a cloud.
Beyond the cloud point, the fuel becomes almost jelly like until such a point, again under laboratory conditions that the fuel blocks a 45 Micron filter, its Cold Filter Plugging Point.
Finally the fuel will reach its Pour Point, in other words it will solidify, stop pouring etc.
Under normal circumstances from point to point, i.e. cloud to CFPP, a delta of 2 to 5 degrees Celsius is standard. It is when these ranges vary beyond 5 degrees when it can be assumed that additives are in play.
Additive Use
As mentioned earlier, one weapon in the armoury of a fuel blender is additives in order to improve the performance of a fuel, one type of which is a middle distillate flow improver (MDFI). These MDFI additives work to improve operability at colder temperatures by depressing both the CFPP and the Pour Point. Cloud Point however is unaffected.
Additives can be added proactively or re-actively and have varying effects depending on the fuel and dosing rate and their effects generally lessen with larger quantities of additive.
So armed with the routine behavior of unadditized fuels when cooling it is feasible to identify fuels with far wider temperature variances from Cloud Point to Pour Point.
Current Position
Recent data available to Integr8 fuels suggests that a large proportion in ARA, North West Europe and ports replenished from this area have a Cloud Point above 10 Deg C and a delta from Cloud to Pour Point of 16 Deg C which takes us to the Winter grade Limit for Pour Point (-6 Deg C). See Diagram below.

The DMA fuels that exhibit such properties are usually identifiable by their higher densities (0.87 to 0.89 Kg/Ltr) as can be seen from the data below, whereby the average delta for such fuels from Cloud to Pour Point is 25 Deg C.

Skaw on the other hand worryingly bucks that trend with fuels with similar poor cold flow operability as ARA exhibiting far lower Densities (0.843 Kg/Ltr) and far better combustion characteristics (54 Cetane Index v 42 in ARA). This results in the specter of even the most eagle-eyed technical manager not spotting what lurks behind the mask.

Therefore both examples would in the eyes of ISO 8217: 2005/10/12 meet the winter grade specification but in real terms could create significant operational challenges onboard the vessel.
Control Measures
So proactively what can be done to minimise risk to the vessel and the end user?
Firstly it is essential to understand the vessel, its uses for distillate fuels, its limitations and its upcoming voyage. Some vessels are more sensitive to cold flow properties than others, for example those with cranes such as a Geared Bulk Carrier or Heavy lift vessel given we would be concerned about ambient air temperatures (& wind chill) rather than simply the sea temperatures.
Secondly it is obvious that this is more of a concern if a vessel is headed to colder climes, for example the Baltic in the middle of winter. Planning is therefore essential to consider whether for example a summer grade fuel picked up in Singapore is fit for purpose in the Baltic in January, I very much doubt it would be.
Finally, and most importantly should risks be identified during procurement then a data driven process of risk mitigation should follow.
Buyers must check during enquiry that:
• Their expectations are clearly passed to their counterparty, for example Cloud Point 0 Deg C Maximum.
• Fuel is guaranteed to 2017 Winter Grade wherever possible which mandates the reporting of Cloud Point and CFPP..
• If the fuel is not guaranteed to 2017 then a Certificate of Quality should be obtained for the batch in question with
Cloud Point or CFPP data provided which meets the requirements.
Inevitably such demands may result in a premium being charged by the supplier, however given the circumstances it is a price worth paying to swerve such fuels.
Conclusion
So to conclude until such time that adequate protection is provided within ISO 8217 it is essential that buyers understand the risk of such fuels and put suitable buffers in place to protect them from issues.
Control measures may be able to be utilized post issue such as more additive or a small amount of heating (which may be possible given some vessels have converted old fuel oil tanks into distillate tanks) but it by no means guarantees a resolution.
The best bet is to plan, purchase smartly and if necessary accept a price premium given the challenges these masquerading fuels bring.
Chris Turner Manager – Bunker Quality and Claims P: +65 6622 0042
E: chris.t@integr8fuels.com
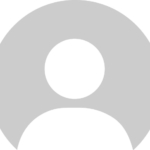
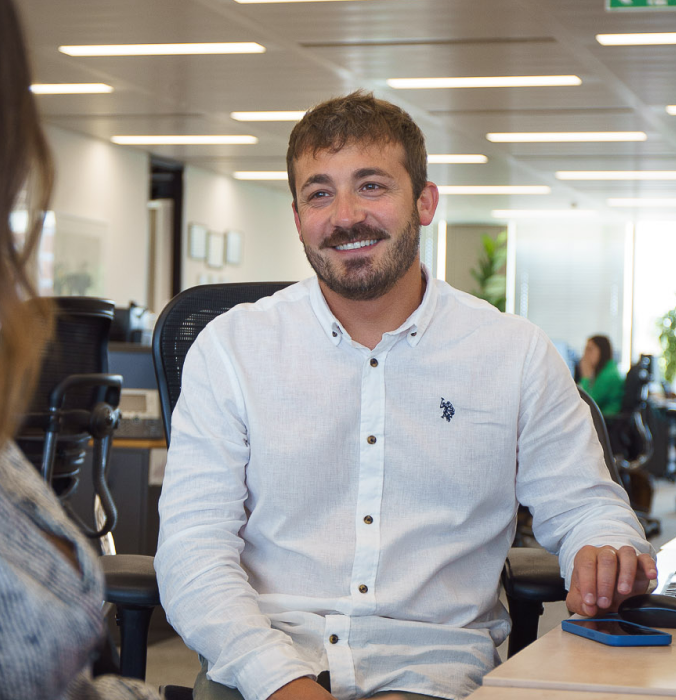
Contact our Experts
With 50+ traders in 12 offices around the world, our team is available 24/7 to support you in your energy procurement needs.